Veel bedrijven hebben in het verleden of heden gekozen voor Rockwell Automation om hun industriële omgeving te automatiseren. In deze omgevingen worden de behoeften per bedrijf steeds unieker en daar moet op ingespeeld worden. Tegelijkertijd komen bij industriële bedrijven steeds vaker IT en OT samen. Wij spraken met Gert Thoonen, die vanuit zijn rol als Security + Process Integration Consultant meer over de ontwikkelingen in de industriële automatisering kan vertellen.
Rockwell Automation ontwikkelt al meer dan 100 jaar oplossingen om het werk in industriële omgevingen te vereenvoudigen en te automatiseren. Door die ervaring heeft het een uitgebreid portfolio opgebouwd, zowel op hardware- als op softwarevlak. Aan de basis staat altijd een Programmable Logic Controller (PLC).
Van PLC tot PAC
De PLC is de industriële computer die acties uit moet voeren en daarmee de productie in beweging brengt. Zo’n PLC wordt geprogrammeerd en in de productieomgeving geplaatst, waarna het precies de geprogrammeerde acties uitvoert. In zijn puurste vorm is de PLC daarmee een automatiseringsstap die nooit fouten maakt. Thoonen noemt als voorbeeld een PLC als aanstuurmechanisme voor een industriële machine die soep maakt. “Je geeft de controller de instructies om de ketel eerst te vullen met water, vervolgens te verwarmen en daarna de groente en de tomatenpuree toe te voegen. De PLC voert de instructies voor het proces nauwkeurig uit, zodat de soep precies volgens het recept geproduceerd wordt.”
PLC’s functioneren echt als het brein van een productielocatie. Deze industriële computers zijn door de jaren heen voorzien van verbeterde hardware en programmeerfunctionaliteit. Uit deze evolutie is de Process Automation Controller (PAC) ontstaan. PAC’s maken PLC’s niet overbodig, maar zijn wel vaak geschikter voor zeer grote automatiseringsprojecten met veel complexiteit. Rockwell Automation levert beide opties.
Industriële automatisering vereist complete aanpak
Hoewel een controller in de visie van Rockwell Automation altijd aan de basis van een automatiseringsproject zal staan, is er voor een complete automatiseringsslag in industriële omgevingen meer nodig. Zo dienen aan de controller ook sensoren gekoppeld te worden. “Met sensoren kunnen we bepaalde zaken detecteren. Ze zijn in de procesinstallatie aanwezig en meten bijvoorbeeld de temperatuur of een bepaalde druk of detecteren dat er een lege fles aanwezig is om afgevuld te worden”, legt Thoonen uit. Als de sensor vervolgens een bepaalde, vooraf gedefinieerde waarde weergeeft, dan zet de PLC een voorgeprogrammeerde actie in werking.
Wat volgens Thoonen ook steeds populairder wordt in de industriële omgevingen, is de inzet van digital twins. Daarmee kan een organisatie stappen zetten om de prestaties en het ontwerp van automatiseringssystemen te optimaliseren. Dit door voor en tijdens het bouwen van de machine een virtuele simulatie te maken. De CAD-tekeningen van machines en de programmafunctie worden in emulatiesoftware gezet, om te kijken hoe de digital twin van de machine functioneert. Op die manier ontdek je hoe de machine beweegt en of zij ook daadwerkelijk het product kan maken. Daarmee bespaar je bouwtijd, aangezien het blindelings vertrouwen op tekeningen niet altijd werkt. Bij het bouwen zonder digital twin zullen bepaalde processen niet verlopen zoals beoogd. Digital twins zijn ook de ideale omgeving om operators te trainen zonder dat ze in de fysieke realiteit schade aanrichten als ze een fout maken.
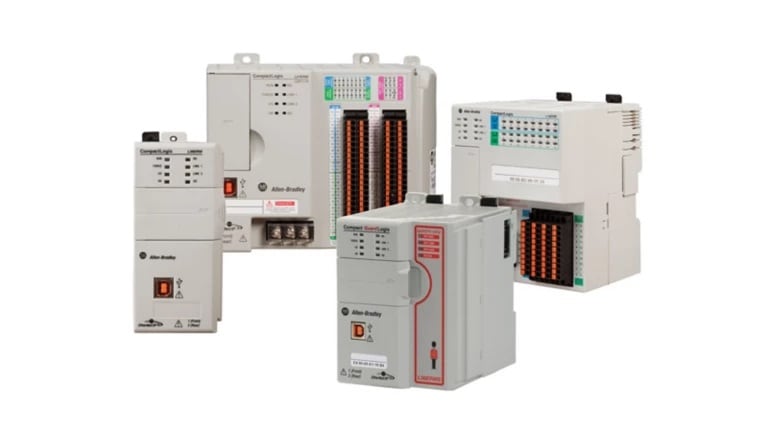
Processen plannen en uitvoeren
Volledige automatisering betekent in de optiek van Rockwell Automation dan ook een combinatie van hardware en software. Een Manufacturing Execution System kan aan de softwarekant zeker niet ontbreken, geeft Thoonen aan. Het MES is een softwaresysteem voor het beheren en uitvoeren van processen en materialen. Binnen de software zijn bijvoorbeeld uitgebreide analyses mogelijk van alle aspecten op de manufacturing-locatie. De analyses signaleren bijvoorbeeld vroegtijdig downtime van een machine, knelpunten in processen om de productiviteit te verbeteren en mogelijkheden om resources maximaal te benutten. Doordat controllers, sensoren en MES-software allemaal over waardevolle informatie beschikken, is de uitwisseling van die data via een koppeling zeer aantrekkelijk.
Deze procesplannings- en uitvoeringsmogelijkheden tillen productielocaties naar een hoger niveau. De productie kan beter georkestreerd worden, terwijl de supply chain met de productie-omgeving verbonden kan worden. Ook zal ieder groot productiebedrijf een integratie van het MES met zijn ERP-pakket willen. Hierdoor kan additionele informatie ingebracht worden, zoals de hoeveelheid benodigde materialen voor het voltooien van een order. Om dat proces te ondersteunen, biedt Rockwell Automation standaard integraties aan met in de industrie veel gebruikte ERP-pakketten van SAP en Oracle’s JD Edwards.
Steeds meer data
Al deze verschillende onderdelen leiden tot een soort nieuwe wereld in industriële omgevingen. Eerst werden machines gemaakt om als kleine eilandjes zelfstandig te werken. Door de nieuwe technologie van de afgelopen jaren generen de machines echter steeds meer data. Als je die data met elkaar combineert, dan kunnen er waardevolle inzichten uitkomen. De data-analyses tonen aan of je de productiedoelen op tijd kunt halen en eventueel nog een extra order aan kunt nemen. Ook het plannen van onderhoud gaat makkelijker wanneer de machine-informatie gecombineerd wordt voor vervolganalyses.
Thoonen ziet de mogelijkheid om veel actueler te werken. “Zonder digitale connecties moesten de data verzameld worden op papier, om ze vervolgens in een Excel-sheet op kantoor in te voeren. Vandaag hebben we de eilandjes verbonden via het netwerk. Alle data zijn beschikbaar en de rapportages over de productie-activiteiten worden automatish gegenereerd en zijn automatisch beschikbaar. Je kunt zo veel betere en accurate beslissingen nemen, want er is real-time informatie in de juiste context beschikbaar. Vroeger had je allemaal aparte systemen, bijvoorbeeld voor planning en de recepten.”
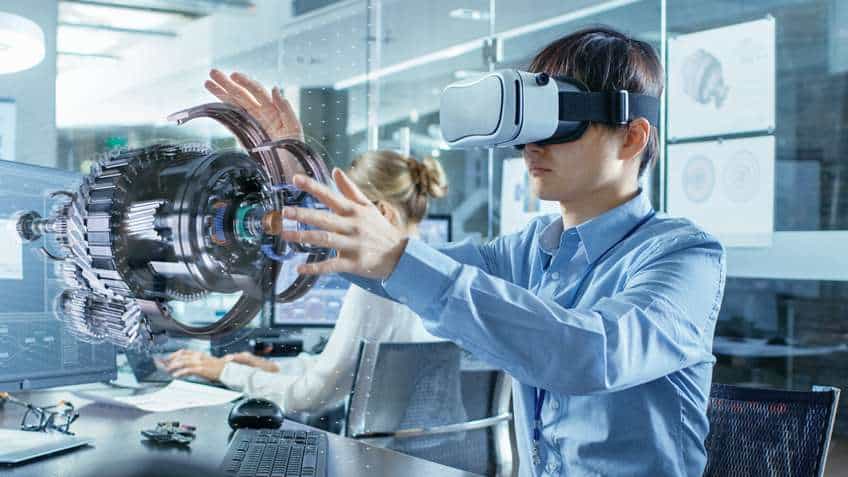
Al die verschillende systemen (silo’s) apart gebruiken is onhoudbaar geworden, wil je als productiebedrijf competitief blijven. De integratie van alle oplossingen heeft de toekomst, om beheer en planning beter te laten verlopen. Alleen op die manier ga je richting volledige automatisering van de industriële omgeving. “Eigenlijk kun je in een productieomgeving met silo’s proberen een hele mooie planning te maken, maar dan ga je ervanuit dat de machine nooit faalt. Die informatie moet meegenomen worden, wil je daadwerkelijk een goede planning kunnen maken”, legt Thoonen uit.
Beveiliging krijgt onvoldoende aandacht
De hele productie-omgeving wordt dus steeds meer met elkaar verbonden. Speciale netwerkprotocollen en veel bandbreedte maken deze hyper-verbonden omgevingen mogelijk. Het verbinden van alle machinale hardware en software levert wat Thoonen betreft echt mogelijkheden voor data en analytics, maar tegelijkertijd ziet hij securityproblemen ontstaan. “De losse eilandjes zijn niet voorzien van de benodigde securityvereisten. Veel bedrijven kopen machines om hun product te vervaardigen en dat zijn enorme investeringen. De leverancier levert de machine met PLC’s en computers en configureert de machine zodat het gewenste product geproduceerd kan worden. De gebruikers durven de machine niet aan te passen omdat ze dat te complex vinden en gebruiken de machine vele jaren lang zonder regelmatige updates van de software of antivirus-programma’s. De gemiddelde lifecycle van een machine ligt tussen de 10 en 20 jaar. Het liefst blijven bedrijven eraf totdat de machine niet meer werkt. Pas dan gaat men proberen te repareren.”
Zeker niet ieder productiebedrijf zal te maken hebben met dit achterstallige securitybeleid, maar de dreiging is wel groot. Steeds vaker worden bedrijven getroffen omdat ze veiligheidsmaatregelen als firewalls, backups en patches niet op orde hebben. Dat is zonde, want het hele securityverhaal kan wel aangepakt worden door traditionele IT-securitymaatregelen uit te rollen in combinatie met een aantal op maat gemaakte industriële beveiligingsaanpakken. De hele productie-omgeving verbinden betekent ook dat er policies en procedures nodig zijn rond mensen, processen en technologie. Idealiter gaan bedrijven de benodigde security in productie-activiteiten beoordelen, om vervolgens nieuwe technologie te implementeren en die ook netjes te onderhouden.
Rockwell Automation gaat dan ook in gesprek met organisaties om te helpen bij het verkleinen van de risico’s en bescherming tegen hackers en ransomware te bieden. Het biedt eigen producten en oplossingen van partners om een totale security-oplossing te ontwikkelen. Zo kan het bijvoorbeeld deep packet inspection aanbieden, waarin verschillende securityfuncties zijn ingebouwd. Denk hierbij aan netwerkinspectie om verdacht verkeer op te sporen en het uitrollen van security-policies.
Automatiseringsreus gaat voor de volledige productie-omgeving
Rockwell Automation is al geruime tijd een vertrouwde partij voor het automatiseren van productie. De PLC staat bij deze automatiseringsslag aan de basis, maar alleen een PLC is niet meer genoeg. Sensoren en actuatoren zoals frequentieregelaars en motor control units, een MES-systeem en digital twins zijn allemaal voorbeelden van essentiële componenten. Tegelijkertijd moet alles zoveel mogelijk geïntegreerd en verbonden worden. Wil je echt real-time inzicht in je productie-omgeving en zoveel mogelijk automatiseren, dan is een stevige focus op integratie noodzakelijk. Hardware, software, IT en OT zijn geen losse eilandjes meer. Voeg je aan dergelijke zaken ook genoeg securitymaatregelen toe, dan is je productie-omgeving klaar voor de toekomst. Daar wil Rockwell Automation zoveel mogelijk bij helpen.